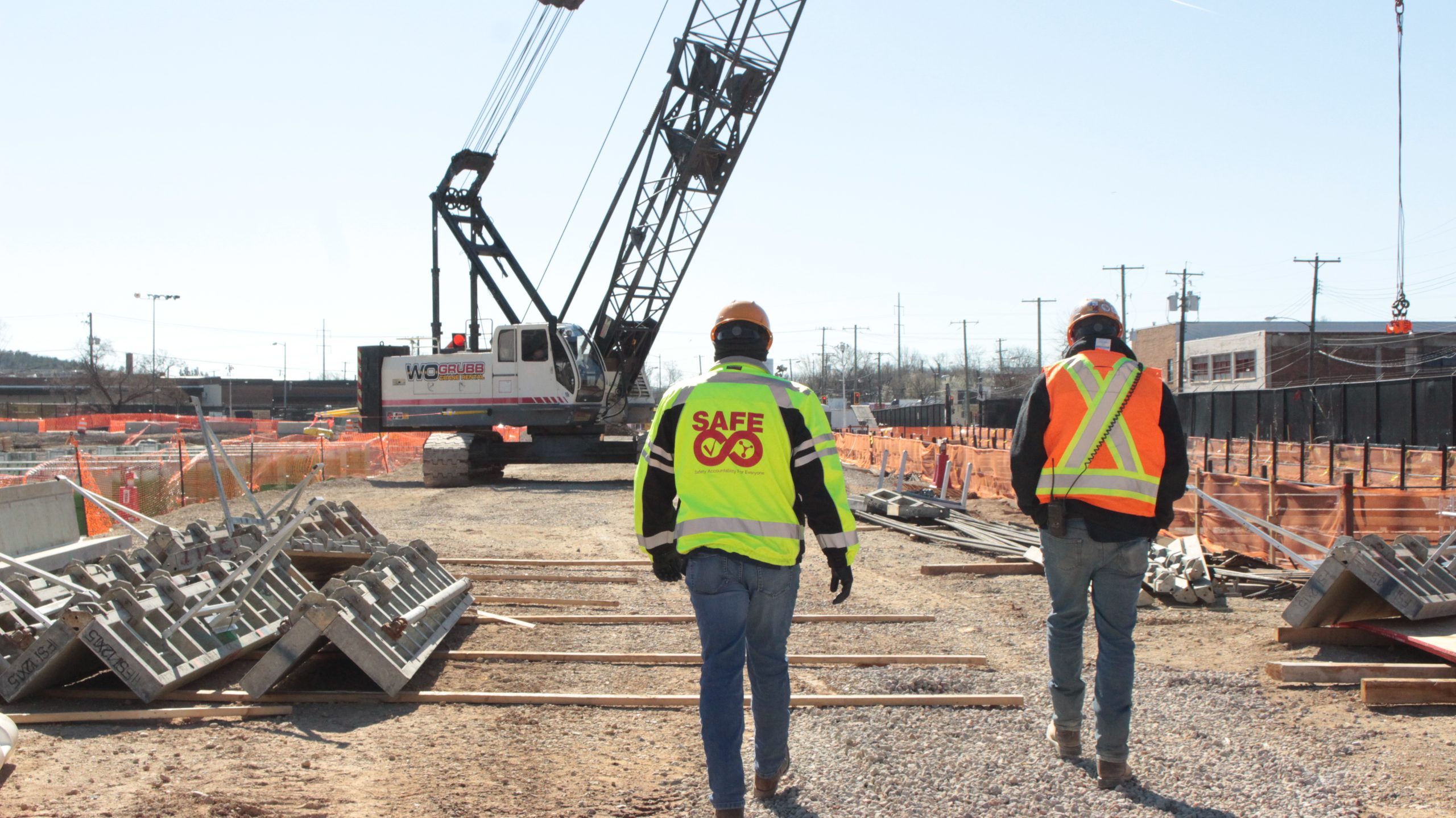
The Bladensburg Bus Garage has served the Washington Metropolitan Area Transit Authority (WMATA) since its initial construction in 1963, and continues to be a vital piece of the Washington, D.C. transit and local community. The Bladensburg Bus Garage Replacement project is the next step in the WMATA transit systems modification plan, and is WMATA’s first endeavor to transition to a 100% zero-emissions bus fleet by 2045. The project is Hensel Phelps’ third design-build bus maintenance facility construction project for WMATA. The inherent knowledge of WMATA’s needs coupled with Hensel Phelps’ application of past lessons learned allowed the design and construction team to identify major design changes early on that will support safety and prevent risk during construction and facility operation.
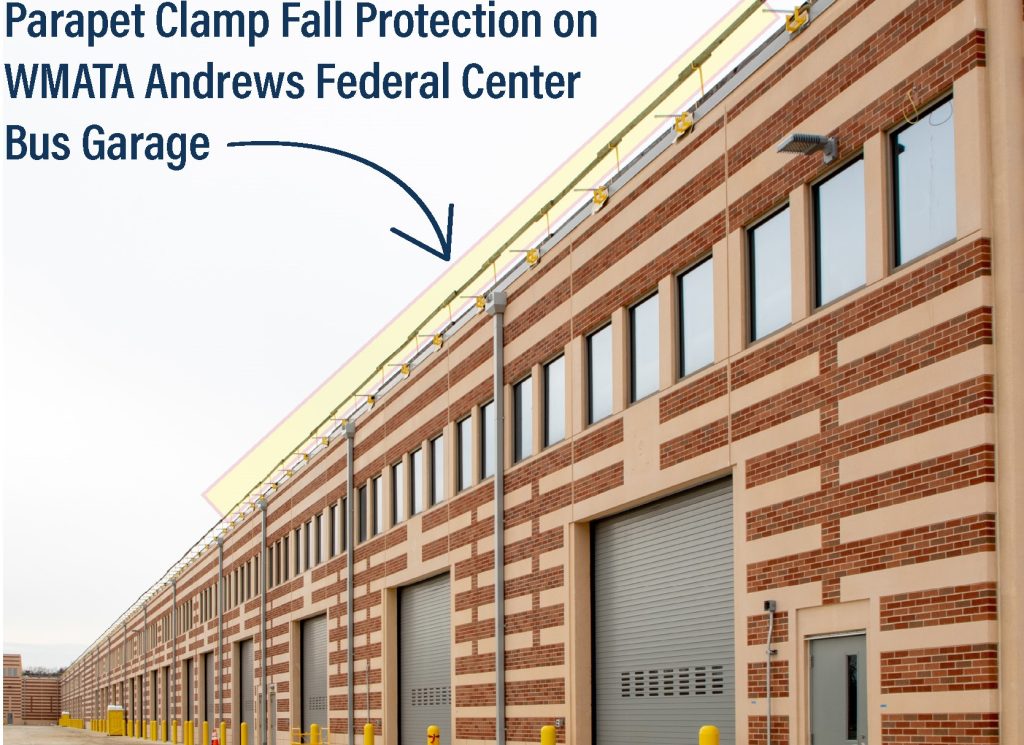
Roof Slope and Parapet Height Designs
The design team’s first challenge was to consider options on implementing fall protection awareness. On past projects such as the Andrews Federal Center Bus Garage pictured above, Hensel Phelps included shallow parapet systems in the design to maximize clients’ cost savings and reduce overall precast on large footprint facilities. However, these systems led to several challenges in construction, resulting in the installation, maintenance and removal of over 5,000 LF of parapet clamps and temporary handrail systems to support construction operations and providing proper Occupational Safety and Health Administration (OSHA) compliant fall protection.
Hensel Phelps and the design team developed a different approach for the Bladensburg project that considered both cost and safety needs. The team modified the design of the roof slope, which strategically increased the project parapet heights and reduced cost to the overall project. This approach benefited the construction team by removing the risk of fall exposures on the roof level once the precast system is erected without the use of personal fall arrest systems, anchorage points or handrail systems. This solution reduces a major risk component that has existed on past projects and maintains the project’s GMP budget.
Inset Exterior Precast Envelope
The Bladensburg Bus Garage design includes a three-story administrative support area adjacent to the bus maintenance and warehouse facilities. This area, having been previously clad with precast, has presented challenges similar to those on past projects. On previous projects, the weight of the suspended panels resulted in larger structural support components which increased cost and created challenging lift plans that involved picking precast at an extended length from the crane positioning over the new building. This resulted in upsized crane selection and specialized planning for hoisting activities, which drove cost of the project and added significant risk due to the weights of these inset panels. The Bladensburg project team worked with WMATA to provide an alternate solution to meet WMATA’s needs, settling on a metal stud frame exterior system with Terracotta paneling to maintain a like design aesthetic. This has reduced the risk of large and potentially critical picks and reduced the weight of the overall structure required to support the original precast panel design.
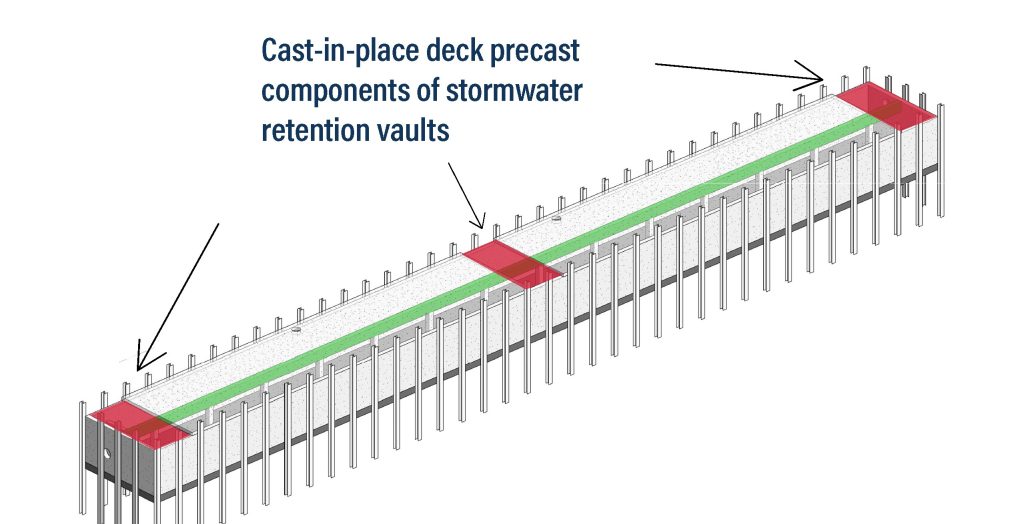
Rainwater Harvesting Tank Access and Ventilation Points
The Bladensburg Bus Garage is designed to achieve LEED Platinum Certification. Due to municipal regulations and the LEED criteria, the project contains two 500,000-gallon cast-in-place below-grade stormwater retention vaults to harvest water for reuse by the building’s bus wash facilities. The construction of these large vaults has presented several challenging scenarios, the biggest challenge being the exposure to confined spaces during concrete deck construction. As a result, Hensel Phelps worked with the design team to include areas of the cast-in-place deck that to implement in final precast components set at the completion of vault construction. This will improve safety during construction by allowing proper access to these confined spaces and the ability for safe rescue. Other benefits of this solution include atmospheric control and the ease of material removal at the completion of cast-in-place components.
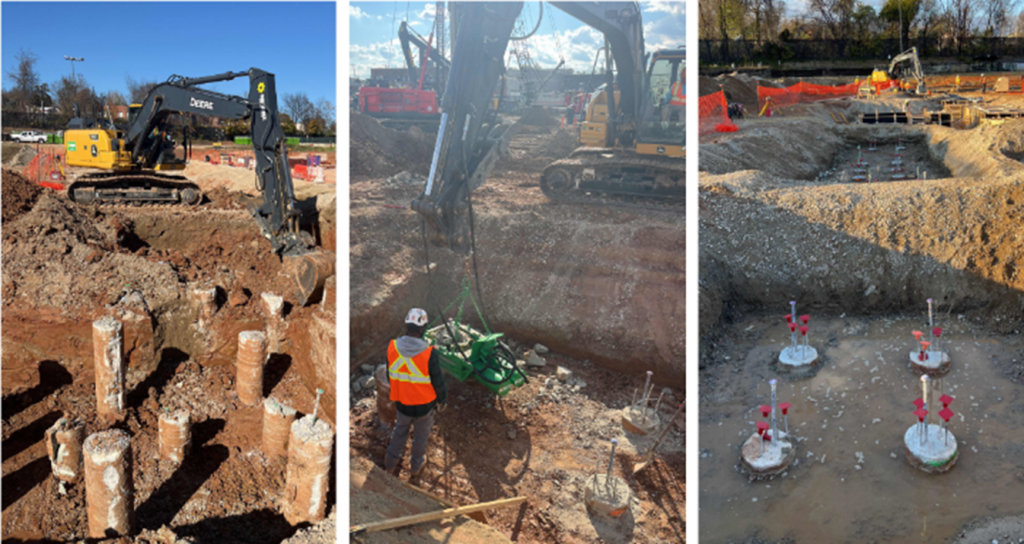
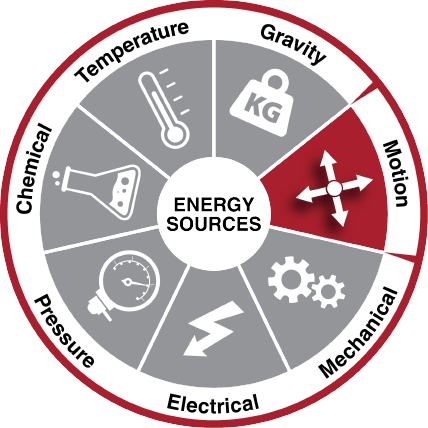
Auger-Cast Pile Cutdown Procedure
The Bladensburg Bus Garage project site is a legacy site of several generations of industrialized buildings in downtown Washington, D.C. As a result, the site has very poor soil conditions that required both remediation and a deep foundation design. At the outset of the project’s design, Hensel Phelps identified the risk of cutting these piles to the proper elevation versus working around the piles before they were cut to grade. The pile cap and grade beam foundation system was designed to be economized with the planned subgrade of the building pad. This allowed the top of the pile cap elevation to be equal to the building pad subgrade elevation, thus limiting the depths of the installations. To ensure both safety and efficiency during this process, the construction team utilized a pile breaker that provided a clean cut, which left a fully prepared surface for pile cap installation. The use of this specialized equipment eliminated the need for labor intensive preparation of the auger cast piles while aiding in keeping the piles cut to grade as they were placed and cured. Hensel Phelps’ solution to cutting the piles reduced potential hazards that could result from working around stationary objects, which was recognized as a motion energy source.